Product Display
Polyurethane Rubber Strip - Urethane Wear Strip
Shanghai Pepsen has been producing polyurethane strips in China since 2004, allowing for customized hardness, formulation, sizes, and tolerance. Polyurethane strip is also called as polyurethane rubber strip or urethane wear strip, to distinguish from urethane foam strip. Vulkollan strip is also available in PEPSEN.
How Does PEPSEN Make Polyurethane Rubber Strip?
1. Compound Preparation: PEPSEN likely starts by selecting the appropriate polyurethane raw materials and compounding them to create a custom formula that meets specific requirements for hardness, flexibility, abrasion resistance, or any other desired property.
2.Molding: If the strips are molded, the compound is poured into pre-designed molds that match the desired profile and dimensions. After the mixture cures, the molded strips are removed from the mold and post-processed as needed.
3. Curing: Whether molded or extruded, the polyurethane undergoes a curing process. This can be done chemically through reaction with heat or time, depending on the type of polyurethane being used. Curing transforms the liquid or semi-solid material into a hard, durable elastomer.
4. Trimming and Finishing: After the polyurethane has cured, the strips are trimmed to the correct length and width if necessary. Additional finishing processes may include sanding, painting, or applying adhesives or coatings to enhance performance or facilitate installation.
5. Quality Control: Each stage of production is likely monitored by PEPSEN’s quality control team to ensure the strips meet stringent standards for consistency, dimension accuracy, and material properties.
Feature & Advantages:
Urethane wear strips, which are typically made from high-performance polyurethane material, are designed to withstand considerable abrasion, impact, and stress. These strips find application in areas that require enhanced wear-resistance and low friction properties.
Applications of Urethane Wear Strip
1. Conveyor Systems: Urethane wear strips are commonly used as guide rails, skirting, and belt scrapers on conveyor belts to minimize material build-up, reduce friction between moving parts, and extend the life of the conveyor system.
2. Material Handling Equipment: In equipment like fork lifts, stackers, and lift trucks, urethane wear strips can be installed on edges and corners to protect against damage from frequent contact with other surfaces, pallets, or goods being handled.
3. Machine Components: As liners, bushings, or pads, urethane wear strips can be used in various machine tools and industrial equipment to decrease wear on sliding or rotating parts, such as linear guides, tracks, and chutes.
4. Doors and Gates: For doors, gates, and hatches in industrial settings, urethane wear strips serve as effective seals and buffers, reducing wear on the doorframe and ensuring smooth operation over extended periods.
5. Flooring Protection: Urethane wear strips are installed at thresholds, ramps, or loading docks to protect floor surfaces from damage caused by foot traffic, rolling loads, and heavy machinery.
6.Agricultural and Construction Equipment: On farm implements, earthmoving machines, and other heavy equipment, urethane wear strips are often used to line bucket edges, blade edges, or any other part that comes into contact with abrasive soil, rocks, or debris.
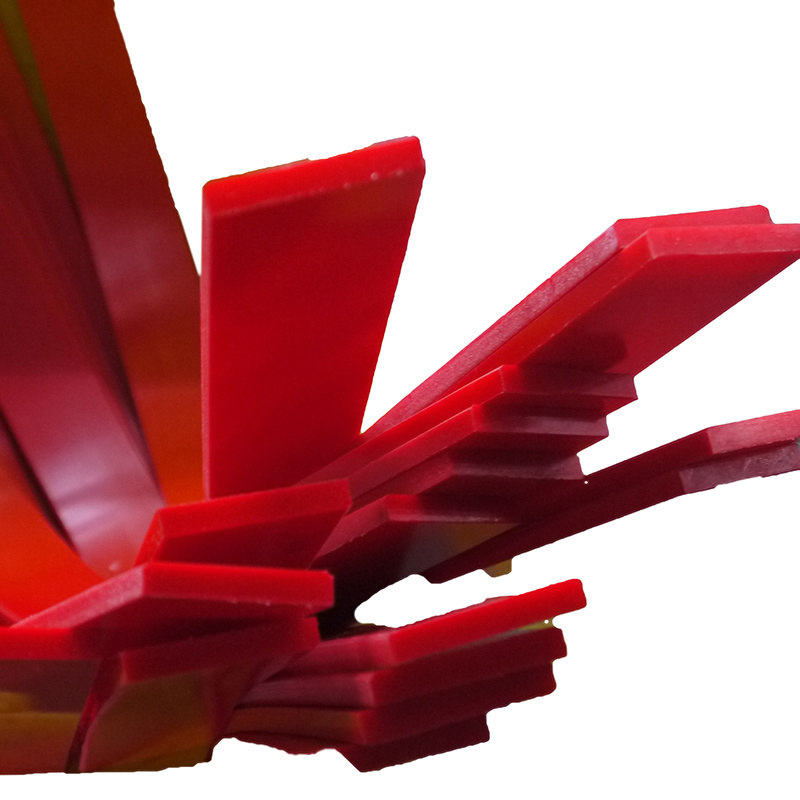
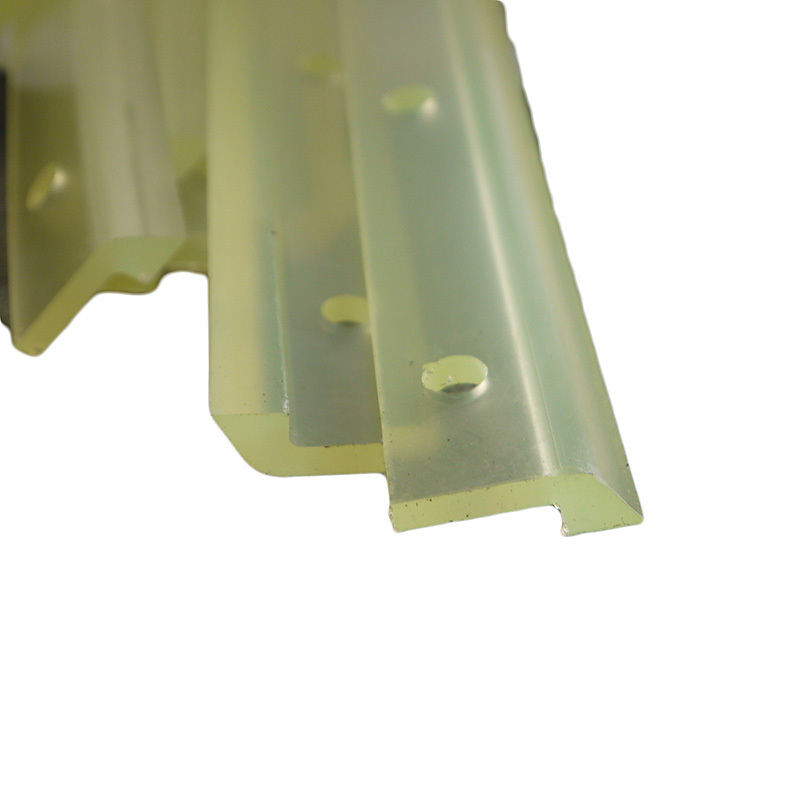
previous
next
previous
next
Product inquiry