POLYURETHANE MACHINING
POLYURETHANE MACHINING
Machinability
Standard procedures used to machine plastics are applicable to polyurethane elastomers.
Key Points to Remember:
1. Polyurethane elastomers have much lower thermal conductivity than metals, so heat generated by cutting tools stays close to the tool and raises the polyurethane temperature rapidly. This heat must be controlled. Melting will occur at approximately 550°F (228°C).
2. Elastic memory—Elastic recovery occurs in polyurethane elastomers both during and after machining, and the cutting tool must provide clearance to compensate for this. Without this compensation, expansion of the polyurethane after cutting will result in increased friction between the cut surface and the cutting tool and, ultimately, in excess heat buildup. Elastic recovery after machining can also result in smaller internal diameters and larger external diameters than were measured during cutting.
3. Modulus of elasticity—Polyurethane elastomers are resilient and can easily be distorted. Because of this, care must be taken to avoid distortion due to holding or cutting forces.
4. Softening point—Gumming, poor finishes and poor dimensional control will readily occur if excess heat is generated and allowed to accumulate. Proper tool geometry, feed rates and cutting speed, in conjunction with coolants, can usually overcome these problems. Water-soluble cutting oils and/or light machine oils are good coolants for polyurethane elastomers.
Useful Tips:
Sawing—Use a band saw with a 4- or 6-teeth-per-inch blade with raker set. Operate at higher speed settings. Apply oil or water as cutting proceeds. Do not force the work.
Milling—Not recommended for grades below 50D in hardness. The harder grades machine similar to aluminum. Tools must be sharp and the work must be securely clamped. Use high operating speeds and low feed rates. Two-flute end mills and single-point fly cutters are preferred.
Grinding—In the lathe, turn the work at low speed. Set the tool post grinder for a feed rate of 0.005 inch per revolution (ipr) and use a 20-80 grit grinding wheel at a surface speed of 6,000–8,000 fpm. Finish the stock removal per pass to a dust-type grind. Use air blasting to clean the wheel and cool the stock. Too much stock removal at one pass results in melting or smearing of the surface. Fine abrasives can be used for final polishing.
Lathe turning and boring—In general, use sharp tools, a high turning speed and a slow rate of feed. Water or plastic lubricants can be used as coolants. Cutting tools for polyurethane elastomers must have sharp, carefully honed cutting edges. Clearances must be greater than those used for metal. High-speed steel or carbide tools are recommended.
Drilling—Slow, spiral drills perform best because the large flute area permits free discharge of chips with a minimum of binding and heat buildup. Retraction of the drill frequently aids in eliminating chip blockage of the flutes. Breakout tearing at the exit side can be reduced by slowing the drill speed at the bottom of the cut or by backing with another material. When drilling a series of small holes, inserting a pin in each completed hole prevents the force of the drill from pushing material into adjacent holes and causing subsequent distortion.
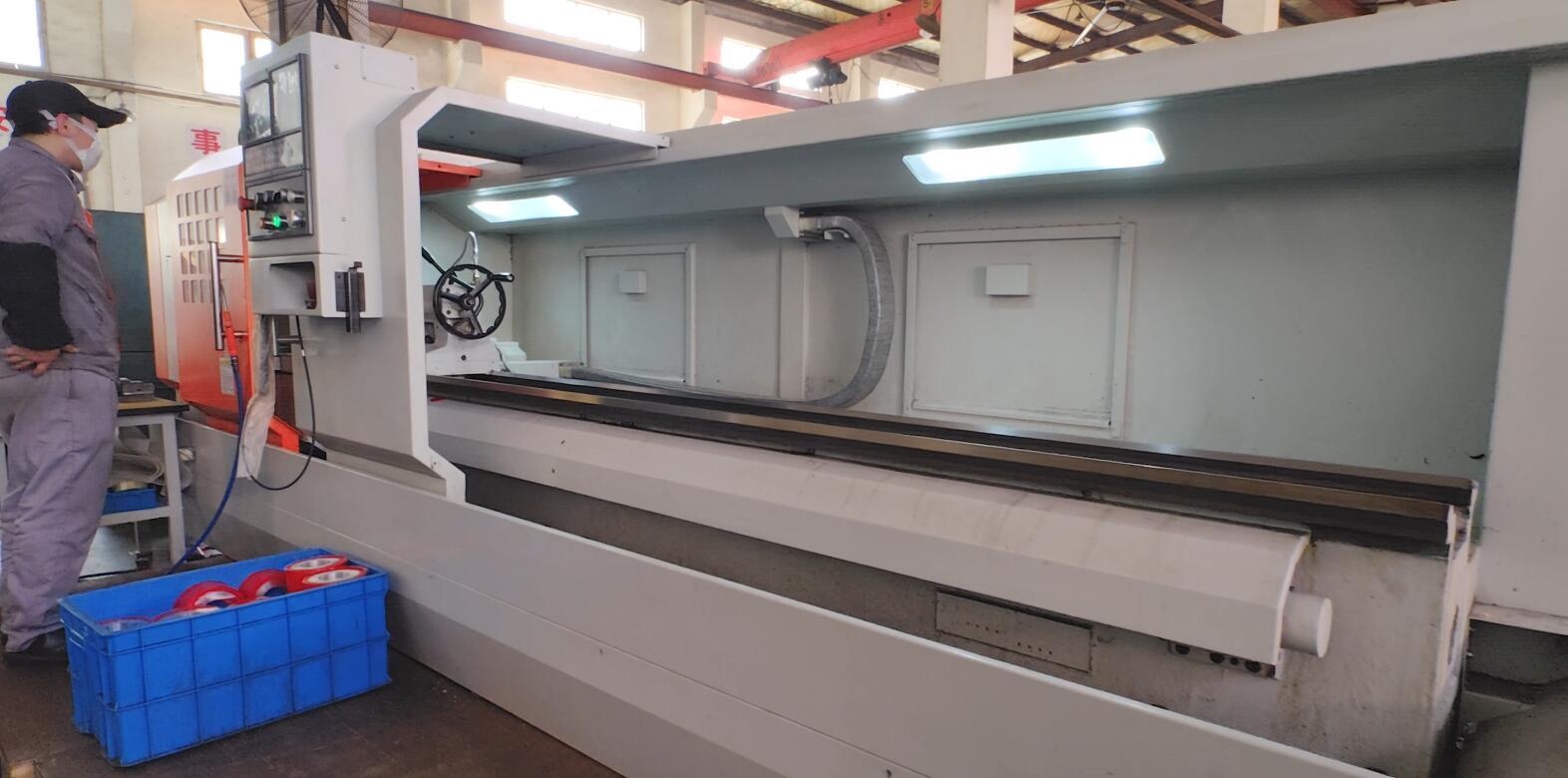
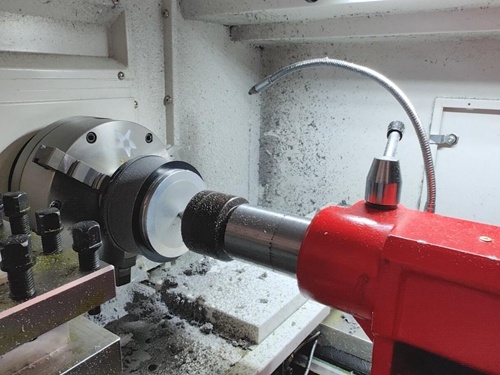