COMPRESSION MOLD CASTING
COMPRESSION MOLD CASTING
Urethane Compression Casting-Superior Dimensional Accuracy
Cast-compression molding is often used for parts that must be molded to tight tolerances and with complicated shapes or small wall thickness. Additional design such as metal inserts can also be over molded. The polymer/hardener mixture is poured into the compression mold and allowed to gel. Pressure is applied to form a gel material and held until the reactants solidify. The optimal time to apply pressure should be determined experimentally for each molding application. Heat is applied through the platform of the press. Generally, mold ventilation is not required.
How Does Urethane Compression Molding Casting Work?
Though sometimes there are different procedures for compression molding, usually three major steps are involved. First, a mold is often designed and manufactured to according to the engineered drawing. A compression mold is always two halves mold which include a bottom mold and a top mold. Afterwards, the mold will be heated and each half of the mold will be casted with polyurethane material. The material will start to solidify after a while, we can close the mold and use a hydraulic press to push out any air bubbles, creating a uniform shape with minimum flash. The mold is kept tightly sealed for a specific period, enabling the material to cure fully into the final shape. Finally, the upper mold is removed, and the part is demolded. This produce a part that will not separate as it is chemically bound to each half during the curing process. This produces parts with complex shapes, without the need for secondary machining process.
How Does A Hydraulic Press Help To Create Superior Dimensional Accuracy?
A hydraulic press can create pressure. The pressure of the closed mold forces the casting polyurethane to fill all areas of the mold while dispelling air, creating a uniform shape with minimum flash, leading to tight tolerances and superior dimensional accuracy.
The Benefits of Compression Molding Casting
•The press applied during this process enable polyurethane to fill the entire mold cavity, leading to precise and fine parts.
•Can avoid flash, sink marks and other defects
•Trimming process is not required
•Compared to other casting process, compression molding is often the most cost-effective and efficient method to produce small and large volumes. Unlike injection molding, this process does not require expensive molds and equipment.
•Tolerances are as tight as injection.
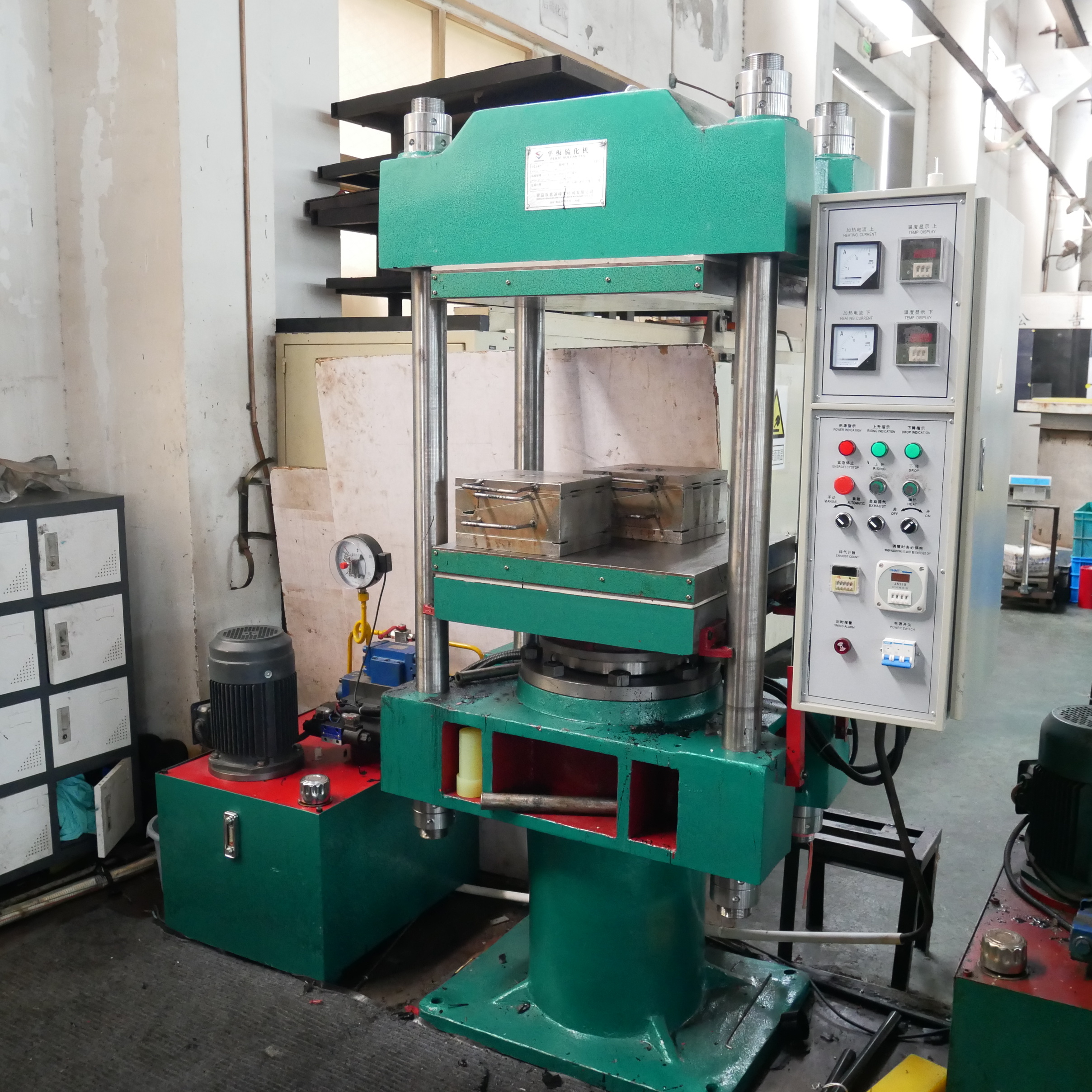
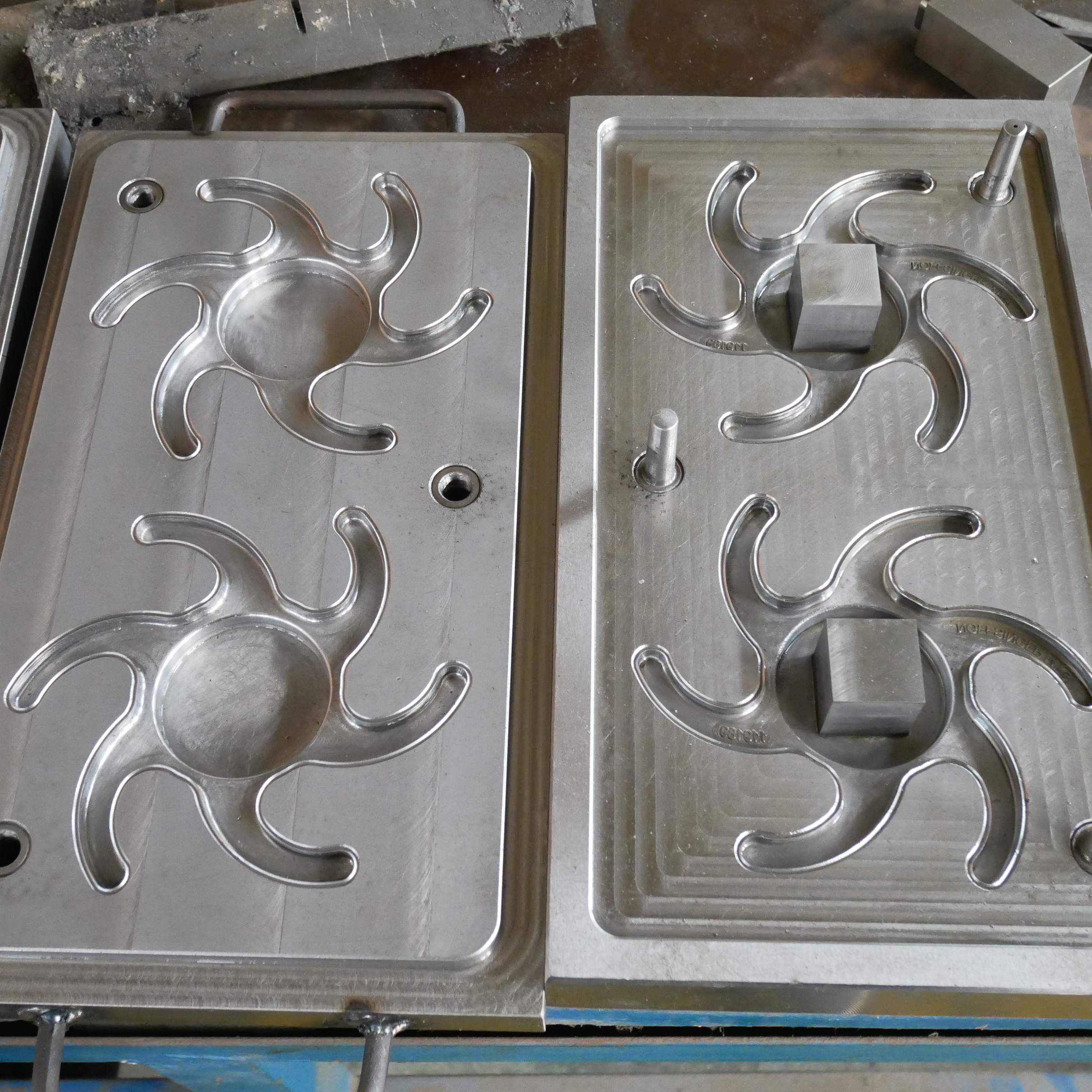