OPEN CASTING
OPEN CASTING
Urethane Open Casting
Open casting is the easiest way to produce polyurethane parts. Pour the prepolymer/hardener mixture into an open mold and keep it there without applying pressure until the mixture solidifies. The main problem with opening castings is to carefully distribute the mixed material to avoid air retention.
With over two decades experience of casting and regular training of workers, all PEPSEN workers are skillful of casting different shape polyurethane parts which can assure high quality and low cost products are delivered to customers.
Open casting is usually used for products with loose thickness tolerance. There will be an open casting “face” that makes air vent easily from liquid during casting and chemical reaction. The casting face can be machined afterwards, so that good finish and tight thickness tolerance can be guaranteed as well.
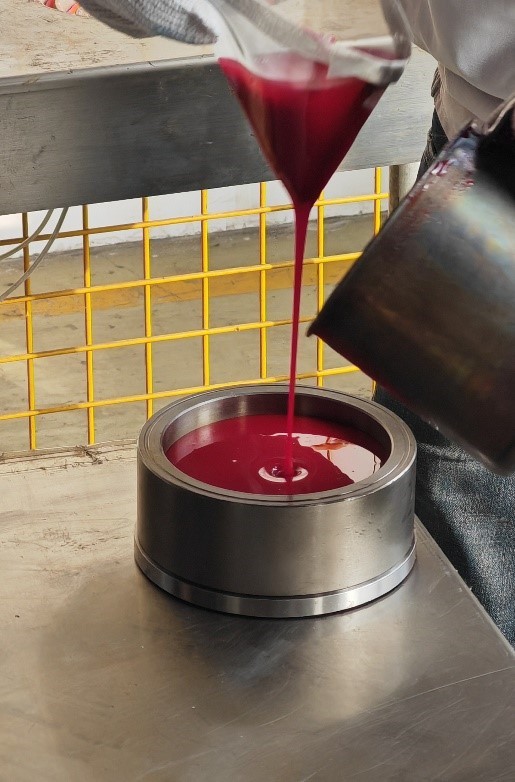
One Basic Principle TO Avoid Air Bubbles
Pouring polyurethane with MBCA as a curing agent makes it easy to make large parts, even though some parts of the pouring can be gelled before the mold is fully filled. For example, parts weighing up to 500 kg poured using a mixer with an emission rate of 6.8 to 9 kg per minute. We should take care to prevent the formation of voids at the braided lines between the fluid and the gel material. If the subsequent pouring takes place within 45 minutes, the newly poured material can be connected to the previous gel material.
Shrinkage of urethane prevents the top surface of an open casting from becoming very flat.
•Trimming process is required
•Sometime post machining is required.
•Tolerances are not as tight as injection, but given the flexible nature of polyurethane, they can meet the requirements of most applications.
•There is no outer pressures of open casting, so fine details are difficult to achieve.
•With the urethane reaction happening in the mold, production efficiency is lower than injection.