Product Display
Polyurethane Vibrating Screen Spray Nozzles
Polyurethane vibrating screen spray nozzles from Shanghai Pepsen are specialized components designed to enhance the efficiency and longevity of screening processes in various industries, including mining, quarrying, aggregate processing, and construction material production. These nozzles play a critical role in maintaining the cleanliness and functionality of vibrating screens by effectively removing adhered particles, preventing clogging, and reducing dust emissions.
How Does Spray Nozzle Work?
Polyurethane spray nozzles exist in diverse shapes and designs, yet they share a unified objective: to efficiently disperse water over the screening surface for effective material washing. Engineered with self-cleaning features, these nozzles are impervious to rust and corrosion, assuring long-lasting performance. They precisely regulate and uniformly distribute the intended water flow without causing damage to your screen media, thus maintaining its integrity.
Constructed entirely without metallic components that could potentially corrode, these robust polyurethane nozzles are capable of enduring high water volumes necessitated by even the most demanding wet screening operations, ensuring unwavering durability and reliability.
Application of Polyurethane Spray Nozzles
•Coal washer
•Magnetic separator
•Sculping screen
•High-frequency vibrating screen
Features & Advantages Of Polyurethane Vibrating Screen Spray Nozzles
•Specifically tailored for wet screening processes and dust suppression tasks
•Built tough and dependable, these polyurethane spray nozzles securely attach to spray bars, resisting dislodgement even under vigorous operation
•Incorporating a one-piece, molded spray orifice design, they guarantee a consistent flow rate and spray coverage across the material layer, enhancing process efficiency
•Eliminating the risk of accidental detachment, the integrated spray fan remains an inseparable part of the nozzle, safeguarding your screen from potential damage caused by misdirected high-pressure streams.
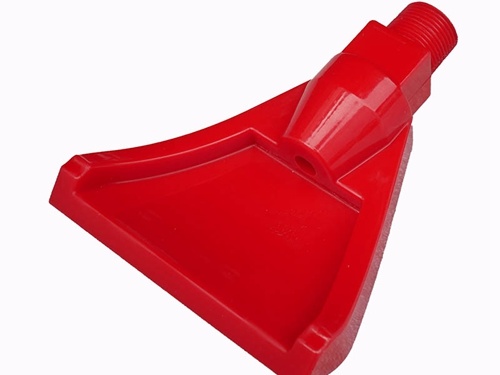
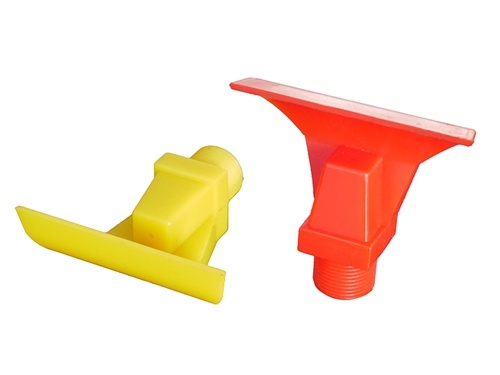
Product inquiry