Product Display
Urethane Coated Drive Rollers
Shanghai Pepsen has been manufacturing polyurethane drive rollers (or called friction rollers) in China since 2004. They are widely used for working environment and applications where the maximum contact surface of rollers against its contact material is required. The material of roller core is usually made of steel, stainless steel, aluminum, bronze, PU as well as other rubbers and plastics.
How To Design The Right Urethane Coated Drive Rollers?
Designing the right urethane coated drive rollers requires a careful consideration of several factors to ensure optimal performance and longevity in the intended application. Here is a step-by-step guide on how to design effective urethane coated drive rollers:
1. Understanding Application Needs: Start by analyzing the specific requirements of your material handling or conveying system. Consider the type, weight, and size of the materials being transported, as well as the speed and frequency of the conveyor. Also, assess the environmental conditions (e.g., humidity, temperature, presence of chemicals), as these factors can affect the selection of the urethane compound.
2. Selecting Core Material: Choose a robust core material such as steel, aluminum, or stainless steel, depending on the load capacity, corrosion resistance needed, and whether the roller will be subject to washdowns or harsh chemicals.
3. Determining Roller Diameter and Length: The diameter and length should be chosen based on the conveyor design, the required tension, and the space constraints. Larger diameters offer better stability and lesser deflection, while length depends on the width of the conveyor belt or material being handled.
4. Choosing Urethane Compoun: There are various types of urethane compounds with different hardness, tensile strength, abrasion resistance, and elasticity. Hardness typically ranges from Shore A (softer) to Shore D (harder). Softer urethanes provide better grip and absorb shock, whereas harder urethanes offer greater durability and resistance to wear. Select the appropriate durometer for the specific application to balance grip, wear resistance, and impact absorption.
5. Thickness of Urethane Coating: The thickness of the urethane coating should be enough to provide adequate protection to the core and to endure the expected wear. Thicker coatings may be necessary for more abrasive or heavier loads.
6. Bearing and Shaft Selection: Ensure proper bearings and shafts are used to allow for smooth rotation and alignment, considering load capacities, speeds, and any special requirements for lubrication or maintenance.
7. Surface Finish: The surface finish of the urethane coating can be tailored for smooth, grooved, or patterned surfaces, depending on the need for extra grip or release properties.
8. Testing and Validation: Before finalizing the design, consider prototyping and testing the urethane coated drive rollers under actual working conditions to validate performance, durability, and compatibility with the rest of the system.
9. Maintenance and Replacement Plans: Think about the ease of maintenance and the expected lifecycle of the roller to plan for eventual replacement, which can influence the initial design choices.
Overall, designing the right urethane coated drive roller involves a collaborative effort between engineers, manufacturers, and end-users to create a custom solution that meets the unique demands of each application.
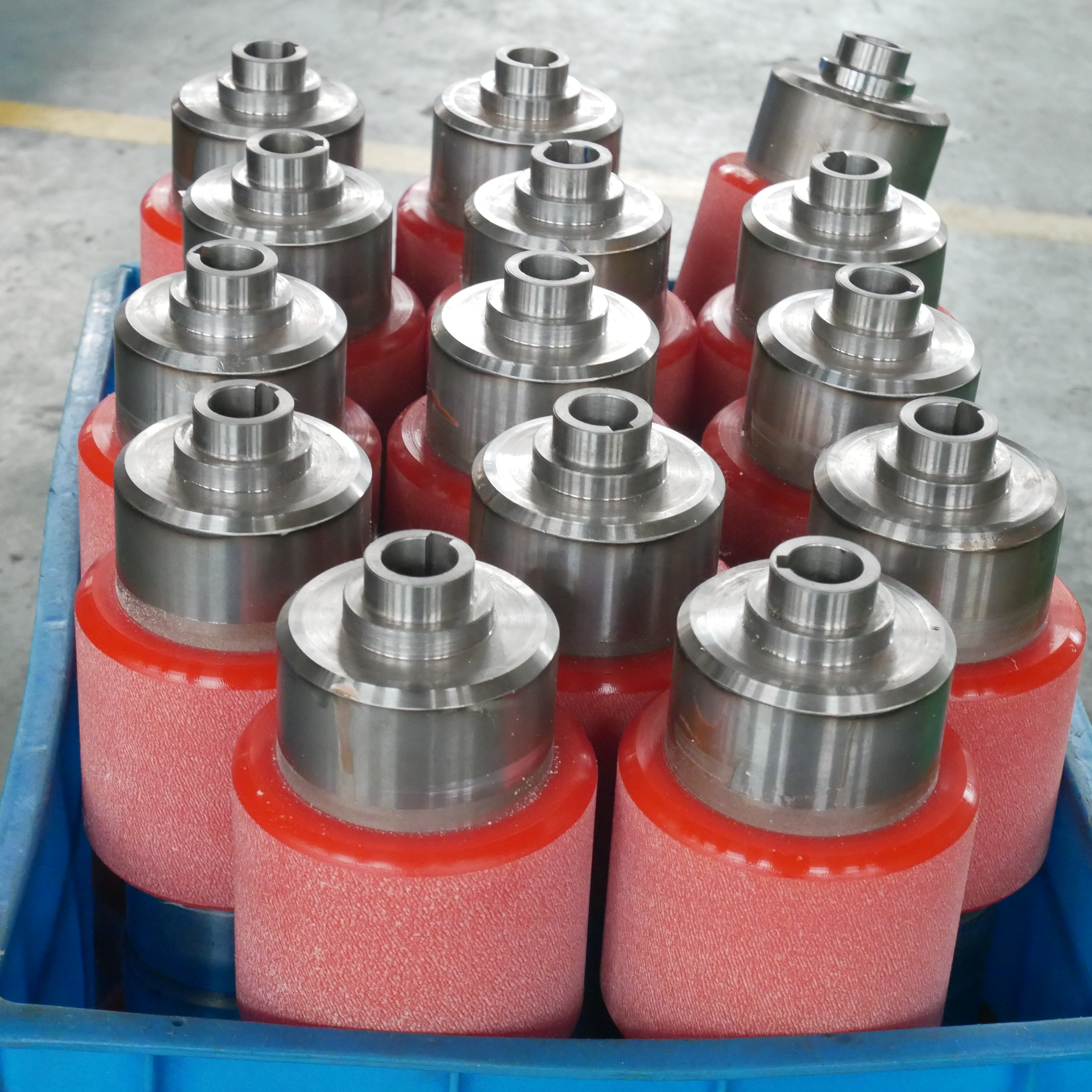
Feature & Advantages:
Our Urethane Coated Drive Rollers boast an innovative design where a robust metal core is coated by thick, resilient urethane. This specialized composition guarantees exceptional resistance against wear, tear, and abrasion, making them the go-to solution for even the most demanding and high-stress industrial environments. The urethane layer, available in a spectrum of customizable hardnesses, delivers optimized grip and traction that significantly reduces product slippage and damage, catering to a wide array of materials from lightweight packages to hefty industrial parts. This tailored functionality ensures not just the safety of your products but also enhances the overall throughput and consistency of your production line. Noise reduction and vibration damping properties: These rollers operate smoothly and quietly, contributing to a more comfortable and productive work environment. Furthermore, the urethane coating's inherent chemical and weather-resistant traits mean our Urethane Coated Drive Rollers maintain their peak performance and aesthetic appeal over time, necessitating fewer replacements and repairs.
Why Choose Us?
By choosing our Urethane Coated Drive Rollers, you're not just investing in a single component, but rather a long-term strategy for enhancing operational reliability, prolonging equipment life, and streamlining workflow efficiency. Whether you're looking to upgrade your current setup or planning a new installation, our Urethane Coated Drive Rollers stand ready to revolutionize your material handling processes, setting new standards for quality, durability, and performance.
Product inquiry